Analysis of fluid-solid coupling at interface of friction pair of high parameter dynamic and static pressure mechanical seal
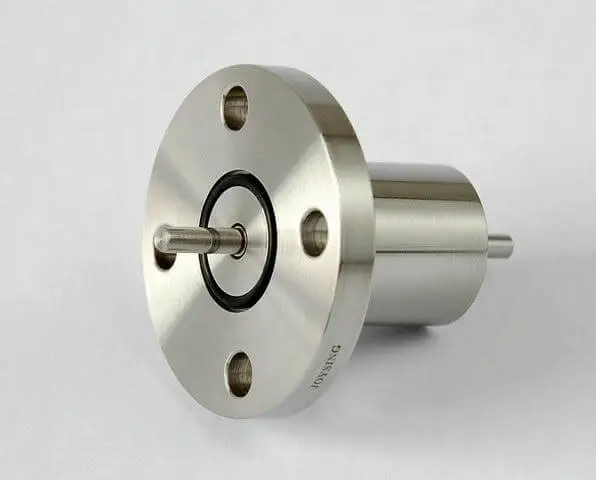
Mechanical seal is a kind of seal with good performance and complicated structure in rotary seal.
From the perspective of the development of sealing technology at home and abroad, with the rapid development of petrochemical, energy, aerospace and other fields, the mechanical sealing performance, service life and reliability under extreme working conditions (high temperature, high pressure, high speed, etc.) are put forward with higher requirements.Hydrostatic and hydrodynamic seals in contactless mechanical seals are widely used because they can achieve controllable leakage without wear or little wear.
Hydrostatic mechanical seal is a kind of hydrostatic fluid film which can be formed by introducing the sealing liquid or the sealed medium into the sealing end face with enough pressure to balance the compression load on the end face and make it have sufficient lubrication and cooling effect on the sealing end face.The working principle of the hydrodynamic pressure mechanical seal is that when the sealing shaft rotates, the lubricating liquid will cause the dynamic pressure of the fluid wedge on the sealing end face and squeeze in between the end faces to establish a layer of end face fluid film to provide sufficient lubrication and cooling for the sealing end face. Extreme conditions under the condition of static seal and dynamic pressure seal sealing characteristics of vice and oil film is different, with high mechanical seal parameter conditions as the research object, to seal and numerical modeling of oil film, and split circular trough of dynamic pressure sealing with ordinary static sealing, comparing the fluid-structure coupling analysis results obtained the dynamic characteristic of the liquid film flow field and flow field characteristics of the influence of the friction pair of stress and strain.
- Basic CFD theory
Fluid-solid coupling analysis is to transfer the results of fluid calculation and the results of solid structure calculation through the interface. The calculation process includes the fluid control equation, the solid control equation and the fluid-solid coupling equation.
1.1 Fluid Control Equation The flow of fluid should follow the law of conservation of physics, which includes the law of conservation of mass, the law of conservation of momentum and the law of conservation of energy.
- Numerical calculation of fluid-solid coupling
The dynamic pressure seal takes the moving ring of the arc-opening groove as the research model. The groove is 2mm deep and belongs to the deep groove. The size of the static seal moving ring is the same as that of the dynamic seal moving ring without the circular groove.Fluid-solid coupling analysis was used to analyze the coupling between the friction pair and the liquid film, and the dynamic characteristics of the oil film between the friction pair and the stress and strain of the sealing ring were analyzed. Finally, the pressure distribution of the liquid film on the end surface, the opening force of the liquid film and the stress and strain of the sealing ring were obtained.
- Results and analysis
Firstly, the liquid film was analyzed to extract the pressure field and temperature field at the interface of the sealing ring, and then the variable boundary condition of the solid structure of the sealing ring was analyzed to calculate the stress and strain of the solid structure. The sealed cavity pressure was 3~5 MPa to analyze the influence of sealed cavity pressure on seal opening force.The rotation speed is 3,000~5,000 r/min to analyze the influence of spindle speed on seal opening force.
It can be seen from the data that the hydrostatic seal liquid film pressure increases from the inside to the outside along the radial direction, and the outer diameter of the liquid film connected with the sealed cavity is the most affected by the pressure of the sealed cavity, and the inner diameter in contact with the air is the least.The strain at the outside diameter of the moving ring is the largest and the strain at the inside diameter is the smallest.
4 Conclusion
The pressure of the liquid film increases from the inner diameter to the outer diameter in the radial direction.The inner diameter of oil film is in contact with air, with minimum pressure.Under the same condition, the dynamic pressure seal liquid film pressure is higher than the static pressure seal liquid film pressure, the static pressure seal dynamic ring outside diameter of the maximum strain, dynamic pressure seal dynamic ring arc groove of the maximum strain.
Both dynamic pressure seal and static pressure seal, seal opening force increases with the increase of seal chamber pressure, under the same conditions, dynamic pressure seal opening force is greater than static pressure seal opening force.
The opening force of static pressure seal and dynamic pressure seal increases with the increase of shaft speed, and increases with the increase of liquid film viscosity. The influence of liquid film viscosity on the opening force of seal is more obvious than that of shaft speed.