Pump Mechanical Seal Installation and Maintenance
Make sure that the mounting chamber is clean and free from foreign matters. The shaft or shaft sleeve matched with the mechanical seal has the correct size, smooth surface and good straightness without hair brake, sharp Angle, mark or deep scratch. Seal the hole in the sealed chamber that is not used during operation. The end face of the sealing chamber must be clean, smooth and perpendicular to the axis line. The two boxes of the horizontal split pump must be well matched, between the two boxes there is a sealing gasket, remove all the sharp corners and burrs on the surface of the sealing chamber. Use the dial gauge to check the accuracy of the shaft. For optimal sealing performance, the maximum allowable misalignment of the shaft is 0.125mm(gross indication deviation). Excessive misalignment may mean damaged bearings or bent shafts. Bute shaft channeling is the minimum, recommended channeling momentum range 0.125mm. Check the pump wear ring and impeller clearance is appropriate. Shaft must rotate freely, friction and improper clearance caused by vibration, can lead to seal damage. When using the bush, ensure that the bush is properly sealed to the shaft to prevent leakage under the bush.
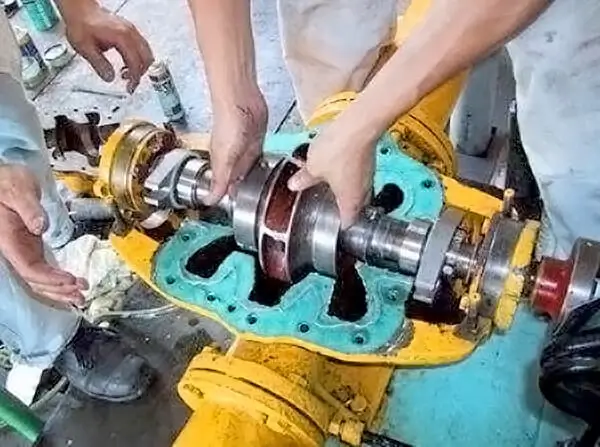
(1) mechanical seals should be carefully handled. It is important to be clean. Do not put the cover down on the floor or on a chair. Carefully read and follow manufacturer’s instructions for sealing installation. Do not open the wrapper until it is ready for installation.
(2) ensure that all mounting screws are fastened. When mounting screws are used as a drive between the seal and the shaft, the shaft shall be reinforced with a hole in the head. Tighten gland bolts. The gland shall be securely fastened without causing the gland to stretch. Use equally spaced gland with 4 or more screws where possible. When securing the gland screw check, use a feeler gauge to check the clearance between the shaft and gland. This is especially important when the gland is not guided by the sealing chamber because the gland must be accurately centered.
(3) before starting the pump, test the seal statically under pressure. Small adjustment can be made to the gland nut to prevent possible leakage at the gland gasket.
(4) do not dry run the mechanical seal. In certain cases, the manufacturer’s instructions for flushing and cooling connections should be followed. Ensure that the suction and discharge ports of the pump are open and that there is a positive level pressure before starting the pump. Do the same when checking for proper rotation and adjusting motor connections.
Prolonging the life of mechanical seals by providing ring sucking control, including requiring that the pumped liquid be maintained at proper temperature and pressure to prevent it from turning solid, steam, or crystallization. Otherwise, mechanical seals may be damaged. For intermittent pump operation, ring sucking control is more important because of frequent start and stop, usually harmful to mechanical seals
Effective maintenance analysis requires the ability to observe changes in sealing performance over a period of time, and the ability to thoroughly investigate the cause of failure and take countermeasures in the case of failure.
(1) spout and burst of seal in operation. Since vaporizable pumps flash as they pass through the sealing surface, specific liquid resting conditions are required and maintained between the surfaces. Check for pressure that requires a flat design rather than a uneven design. If the seal has been balanced, the pressure may have seriously exceeded the value specified in the specification. Determine the correct actual gauge pressure, temperature, and specific weight of the material and, in these cases, the vaporization pressure of the product being processed, as this data may provide clues to troubleshooting.
(2) Seal leakage and icing phenomenon in the gland field. Because of vaporization, the product flashes when passing through the sealing surface. If frozen, no doubt there is damage to the static seal and carbon ring. If possible, these surfaces shall be inspected and serviced and, if necessary, replaced following changes in vaporization conditions.
(3)Seal and drip steadily. Check that the gland gasket is properly pressed against the packing surface. For horizontal split pumps, check the sealing of the joint surface and gland. The gland surface may be deformed or uneven, and improper distribution of the gland screw or excessive bolt force may cause deformation of the static seal, which mainly occurs in the type of seal with fixed edges. The contact portion of the shaft on the rotating member or stationary ring seal may be damaged during installation. Wear surfaces may be caused by abrasive or other particles. If it is integral assembly or installed on the pump sleeve seal, leakage may come out from under the shaft sleeve. Note that sometimes new seals leak when they are first put into service, but the leakage will gradually decrease after several hours of operation.
(4) Sealing vibration sound. Seal ringing indicates that the seal may be in a dry running state without liquid lubrication. It may also be necessary to introduce a circulating flushing pipe from a drain or an external liquid source, if one has been installed, which may be too small.
(5) The rotating surface has powder, shown on the sealing outside of the gland and along the shaft. Insufficient liquid in the sealing surface, due to flash evaporation of vaporized liquid, leaving small residual crystalline particles between seals, or dry contact, and even grinding. From the design of the seal, it is obvious that the pressure of the seal chamber is too high, and re-balancing the seal pressure may be the answer.
(6) Seal leakage and no obvious failure here. The surface may be uneven, which can be determined by removing the underside and checking the wear pattern, or the static seal may be deformed due to excessive gland screw pressure clamping and bending at the same time. This can also be determined by examining wear patterns. Improper connections to the pump outlet and inlet lines can actually stress the pump, and alignment of the shaft may also bend the sealing surface. If this problem is encountered, most of them are vertical suction end lift impeller centrifugal pump. Many of these pumps are designed to be understrength, for example, in order to accommodate excessive weight due to misalignment, which will affect the seal. Pipe supports are the only solution to this problem. The possible causes of shaft vibration are dislocation, impeller imbalance, cavity and damaged bearings.
(7) Short sealing life. The main reason for the short sealing life is that there is too much friction between the surfaces and causes fast rubbing. The friction source may come from the mud, or from the quenching of the supersaturated solution, or from the flash evaporation of the liquid between the sealing surfaces, resulting in the crystallization of the dissolved solid between the surfaces. When this happens, cool or heat. These conditions will be alleviated by ensuring circulation of the pump fluid from the discharge outlet to the stuffing box or clean external flushing.
(8) Equipment dislocation, connection pipe stress bending. Bypass flushing or circulation may be required when the seal appears to be overheating. Inspect seals along shaft for possible wear. Intercepting bushing and poor guide gland often cause these conditions. Check all flush lines and through holes to make sure they are unobstructed, clean, and not blocked, reducing heat by increasing the capacity of the cooling line or expanding the size of the hole in the circulation line. It is also possible that an improper seal type was chosen.